Your Guide to Plastisol Coatings
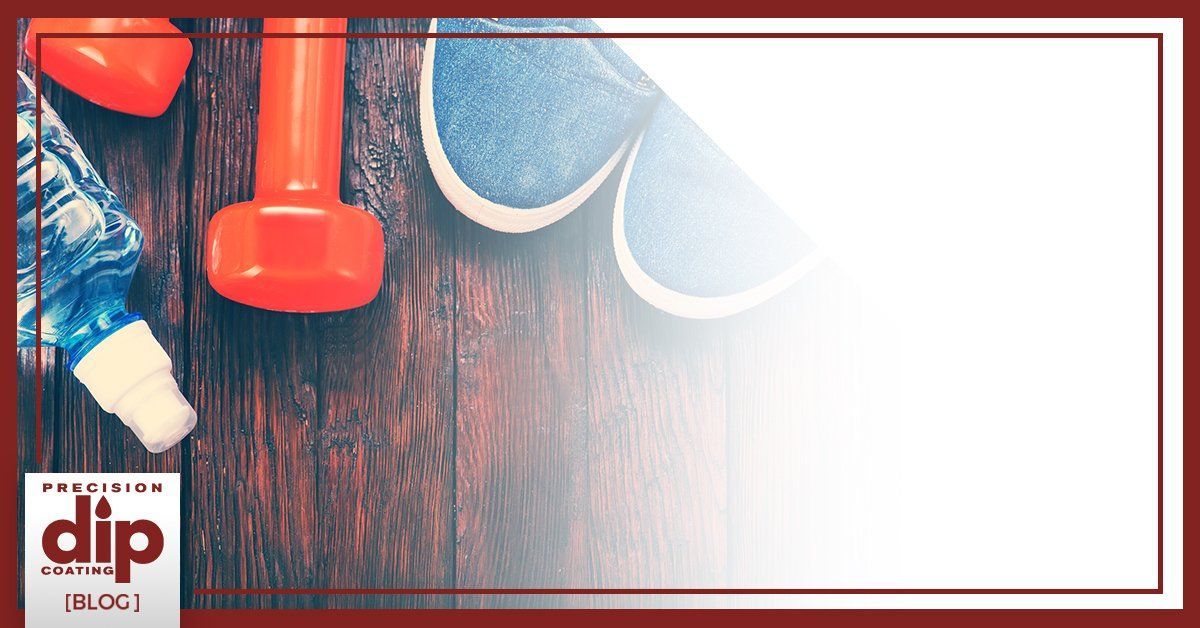
Cost-effective, flexible, and highly resistant, Plastisol is a popular vinyl-based plastic coating with applications across many industries from electrical and automotive to medical and aerospace. Plastisol coatings commonly find uses as varied as tool handles, electrical component insulation, and playground equipment. With so much to offer, there's a lot to know about this versatile plastic.
What Is Plastisol?
Plastisol is a mixture of a polymer, usually polyvinyl chloride (PVC) and a plasticizing compound (adding stretchiness) which can be used as a coating or poured into molds.
How Are Plastisol Coatings Applied?
Plastisol can be applied as a dip or spray coating to heated parts, with special techniques such as slush molding and rotational molding available to coat concave and hollow areas. After coating, parts and products must be heat cured to fuse the plastisol to the substrate.
Advantages of Plastisol Coatings
Quick, easy Plastisol coatings offer countless benefits in protection and usefulness, including:
- Resistance - Plastisol is widely recognized for its superior resistance to many hazards including chemical exposure, corrosion, moisture, mold & mildew, impacts, and electricity.
- Temperature Tolerance - Plastisol performs well in temperatures down to -35°F and as high as 200°F, with an extended temperature range for some formulations.
- Cost - Inexpensive and long-lasting, with minimal waste, the benefits of plastisol coatings far outweigh their minimal cost.
- Longevity - Plastisol coatings are not only long-lasting, they extend the lifetime of the products and parts they protect, too.
- Customizable
- Plastisol can be formulated to match nearly any color, texture, and finish. Additives are available to enhance many of its qualities from hardness and flame retardant to UV resistance, and antimicrobial protection.
Disadvantages of Plastisol Coatings
Plastisol is so versatile and durable, it has very few drawbacks, notably only:
- Substrate Choice - Because coated parts must generally be heat cured, substrates which cannot tolerate curing temperatures (generally around 300-400°F) aren't suitable for plastisol coatings.
- Thickness -While temperature and coating speeds can be adjusted to create differing thicknesses of plastisol, they are still generally a little thicker than some other plastic coatings.
With so many advantages and nearly endless versatility, it's easy to see why Plastisol is one of the most popular plastics for dip and spray coating. At Precision Dip Coating, we have decades of experience working with Plastisol and other plastics with dozens of industries.
Contact us today so we can help you with a plastic coating solution.