Electrical Dip Coating for Fire Safety and Reliability
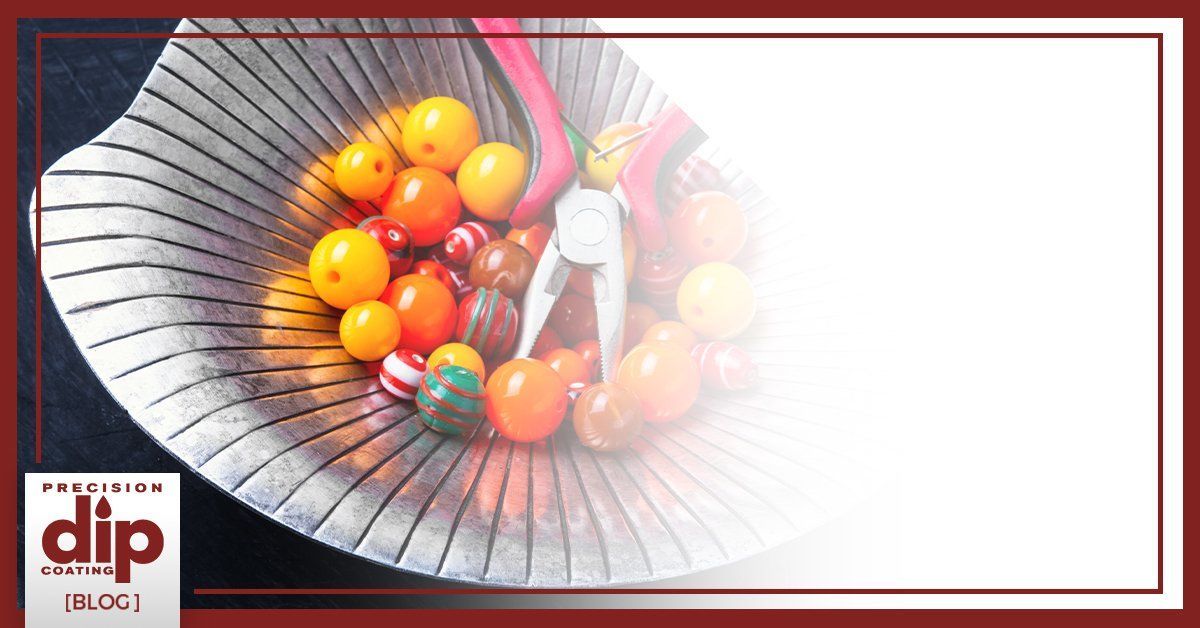
Electricity plays a crucial role in our lives and using it safely is of paramount importance. Because plastic is an excellent insulator, it is a tried-and-true material for protecting people from electrical shocks and protecting component parts from each other. Precision Dip Coating has over 30 years of industry experience and expertise to provide safe, appropriate, cost-effective dip coating for your electrical and other needs.
What is Electrical Plastic Coating?
Electrical plastic coating serves to both protect electrical components from moisture and dust, and to prevent unintended contact between components, arcing, shorting, or contact with people. In short, electrical plastic coating keeps the electricity in and everything else out. Electrical applications of plastic coating can be used in everything from bus bars and underground tap connectors to electrical switches and high voltage tools. Types of electrical plastic coating include Vinyl, Plastisol, Nylon, and Epoxy and can be applied as liquid vinyl dip, electrostatic spray, or fluid bed powder coating.
How Does Electrical Dip Coating Prevent Dust and Lower Risk of Fires?
Dust can easily catch fire with even a single spark, so protective plastic coating can prevent dust from ever coming into contact with the electricity carried through wires and other components. Preventing sparks and limiting electrical contact with flammable materials will greatly reduce fire risk from electrical components. Additionally, electrical dip coatings can be flame retardant or dissipate static electricity, enhancing its role as a safety feature.
Why Choose Electrical Dip Coating?
Electrical dip coating is especially effective at treating parts which have a lot of nooks and crannies or are otherwise difficult to coat with spray or other approaches. It can also be more cost effective to dip coat wires and other open components instead of spray coating which would waste a lot of the coating material.
Call the Professionals!
Dip coating of electrical components requires skill and expertise to determine the appropriate coating material for a job, ensure the correct formulation, and apply the relevant techniques. Improperly done, coatings can be full of dips and sags. With over three decades of industry experience, Precision Dip Coating has the knowledge and skills to do a careful, effective job at a reasonable price and in compliance with relevant industry specifications.
At Precision Dip Coating, our specialty is coating and molding. We bring that expertise along with value added services and fulfillment solutions to make your electronic components safer and better protected. Contact us today to see how we can work together.